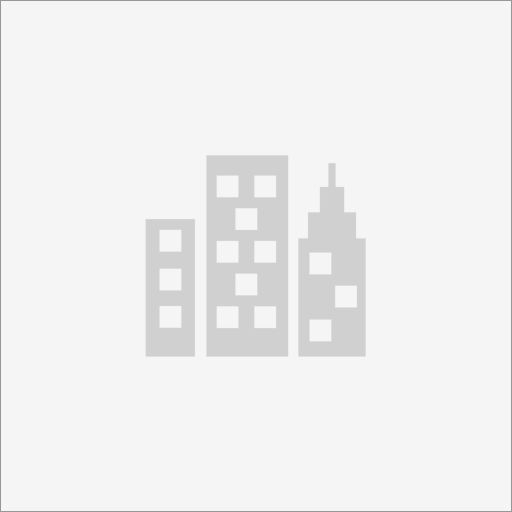
First Class Recruiting
Position Overview
The role is focused on managing specified projects and leading Advanced Product Quality Planning (APQP) activities. It involves coordinating all post-molding activities during the project launch phase, such as trials, and overseeing the finalization of work-in-progress (WIP) and client-specific packaging solutions. The individual will ensure trial processes are thoroughly prepared and assess their effectiveness.
Key Duties and Responsibilities
– Oversee projects from initial conception to completion.
– Lead internal APQP meetings and address issues related to assigned projects.
– Develop Process Failure Modes and Effects Analysis (PFMEA) and control plans in line with new manufacturing protocols for launches.
– Manage launch processes, including efficiency tests and process development (masking, degating, assembly, and packaging), and all pre-production activities after molding.
– Design and implement new layouts for cells and plants, along with work and packaging instructions.
– Use CAD and other technologies to enhance layout, workflow, and inventory management efficiency, initiating improvements where necessary.
– Supervise suppliers for successful commissioning and approval of post-molding machinery and packaging, for both in-house and client use, covering reusable and disposable options.
– Organize reviews and approvals of equipment, processes, and packaging between plants and with clients.
– Prepare for and evaluate trial runs, communicating outcomes as required.
– Collaborate with scheduling and program management teams for trial planning.
– Participate in internal improvement initiatives and document R&D activities for claiming purposes.
– Adhere to standards and regulations related to quality, health, safety, and environmental practices.
– Ensure a clean and safe working environment is maintained.
– Foster a team-oriented atmosphere.
Experience Requirements
– Experience in launching and supporting secondary equipment or automation within a molding context is preferred.
– 3-5 years of experience in the automotive manufacturing industry.
– Familiarity with PLC programming, vision systems, and 6-axis robots.
– Proficiency in integrated manufacturing technology, project management, and understanding of manual and automated assembly processes.
– Effective communication skills, both written and verbal.
– Proficiency in Microsoft Office suite, especially Excel.
– Experience with AutoCAD and 3D modeling software (Solidworks preferred).
Training Requirements
– WHMIS/MSDS, quality, environmental, health, and safety policy training, along with company policy awareness.
– New Employee Orientation, as needed.
– Advanced Product Quality Planning (APQP), Production Part Approval Process (PPAP), and Process Failure Mode and Effect Analysis (PFMEA) training.